Transfer Valve Vs. Diverter Valve: Key Differences
02-03-25
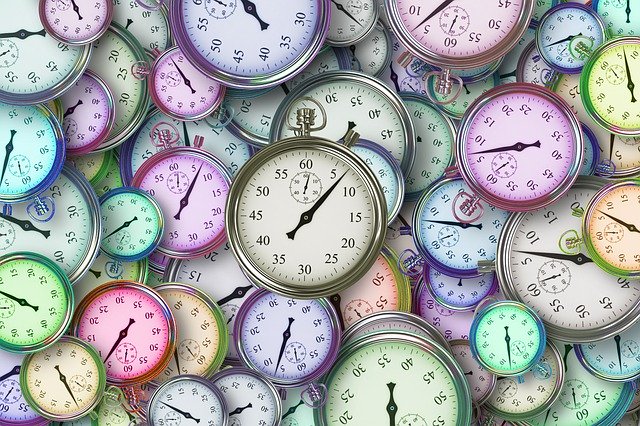
Choosing between transfer and diverter valves can improve your fluid handling system’s performance. While both direct flows, their distinct capabilities serve different applications across industries. Last month, one of our customers learned this the hard way when an incorrect valve choice led to a costly production delay in their chemical processing plant.
At Everlasting Valves, we’ve spent decades helping engineers and facility managers select the correct valves for their needs. Understanding the key differences between transfer and diverter valves isn’t just about technical specifications—it’s about ensuring your system operates at peak efficiency while maintaining safety and reliability.
This comprehensive guide breaks down the essential distinctions between transfer and diverter valves, their applications, and how to choose the right one for your operation. Whether you’re designing a new system or upgrading existing infrastructure, we’ll help you make an informed decision.
Understanding Transfer Valves
Transfer valves serve as the workhorses of fluid control systems, directing flow between multiple ports with precision and reliability. Their design allows seamless switching between different flow paths, making them essential in applications where fluid streams must be redirected without cross-contamination.
At their core, transfer valves operate through a mechanism that creates distinct flow paths within a single valve body. The most common types include:
- Single-port transfer valves: Direct flow from one inlet to a single outlet
- Multi-port transfer valves: Handle multiple flow paths simultaneously, ideal for complex processing systems
- Rotary transfer valves: Use rotating elements to switch between flow paths, offering quick transitions
In industrial settings, transfer valves prove invaluable for:
- Chemical processing plants requiring precise material handling
- Food and beverage production lines needing clean-in-place capabilities
- Pharmaceutical manufacturing, where product integrity is crucial
- Power generation facilities managing multiple fluid streams
The primary benefits of transfer valves include their ability to handle high-pressure applications, maintain tight seals, and operate reliably in demanding environments. Their robust construction, typically featuring hardened materials and self-lapping capabilities, ensures extended service life even in abrasive applications.
One unique advantage of transfer valves is their adaptability to automated systems. Modern transfer valves often integrate seamlessly with digital control systems, allowing for precise timing and remote operation. This capability makes them particularly valuable in continuous processing operations where manual intervention needs to be minimized for safety and efficiency.
Understanding Diverter Valves
Diverter valves control flow direction in lower-pressure applications, commonly found in residential and light commercial plumbing systems. Their straightforward design makes them ideal for redirecting water flow between different outlets, like shower heads and tub spouts.
The main types of diverter valves include:
- Push-pull valves: Simple manual operation for basic flow switching
- Rotary diverter valves: Allow selection between multiple outlets
- T-type diverters: Common in shower systems for dual-outlet control
These valves excel in applications such as:
- Multi-head shower systems
- Pool and spa equipment
- Irrigation systems
- Simple process water diversion
Diverter valves offer cost-effective flow control through their simpler construction and operation. While they typically handle lower pressures than transfer valves, their reliability and ease of maintenance make them the preferred choice for many residential and light commercial applications.
A key advantage of diverter valves is their user-friendly design. Most operators can quickly understand and manipulate these valves without specialized training, making them ideal for consumer-facing applications where simplicity is crucial.
Key Differences Between Transfer Valves and Diverter Valves
Feature | Transfer Valves | Diverter Valves |
Pressure Rating | High (>1000 PSI) | Low to Medium (<500 PSI) |
Construction | Heavy-duty materials, complex internals | More straightforward design, standard materials |
Cost | Higher initial investment | More economical |
Applications | Industrial processing, chemical handling | Residential plumbing, light commercial |
Control Options | Manual, automated, remote | Primarily manual operation |
Maintenance | Regular professional service | Simple DIY maintenance |
Transfer valves excel in industrial settings where precision and reliability are paramount. For example, a petrochemical plant uses transfer valves to control the flow of different chemical streams during processing, ensuring zero cross-contamination. These valves handle corrosive
materials and high pressures while maintaining tight seals.
Diverter valves, by contrast, shine in everyday applications. Consider a modern bathroom with a diverter valve smoothly switching water flow between the showerhead and handheld sprayer. Their straightforward operation and maintenance make them ideal for these consumer applications.
The choice between these valve types ultimately depends on your specific requirements for:
- Operating pressure
- Flow control precision
- Automation needs
- Maintenance capabilities
- Budget constraints
Choosing the Right Valve for Your Application
The selection process begins with an analysis of system requirements. High-pressure industrial applications handling hazardous materials typically require transfer valves, while diverter valves better serve simpler flow control needs.
Key selection factors:
- Flow rates and pressure requirements
- Material compatibility
- Control system integration needs
- Maintenance resources available
- Long-term cost considerations
Decision flowchart:
- High pressure (>500 PSI) → Transfer valve
- Corrosive materials → Transfer valve with appropriate materials
- Basic water flow control → Diverter valve
- Multiple flow paths with automation → Transfer valve
- Simple manual operation needed → Diverter valve
For optimal performance, match the valve specifications precisely to your application requirements, considering current needs and future system expansions.
Proper Maintenance and Care of Transfer Valves and Diverter Valves
Regular maintenance ensures optimal valve performance and prevents costly system failures. For transfer valves, establish a quarterly inspection schedule focusing on seal integrity, actuator function, and signs of wear. Check for unusual noises, leaks, or resistance during operation that might indicate developing issues.
Key maintenance practices for transfer valves include:
- Lubrication of moving parts according to manufacturer specifications
- Inspection of seals and gaskets for wear or damage
- Testing of automated control systems
- Cleaning of valve internals to prevent material buildup
- Documentation of maintenance history and performance trends
Diverter valve maintenance, while more straightforward, remains crucial for system reliability. Monthly visual inspections can catch common issues like mineral buildup or handle looseness before they cause failures. In complex water areas, descaling treatments prevent internal blockages and ensure smooth operation.
Common troubleshooting scenarios:
For Transfer Valves:
- Slow actuation: Check pneumatic pressure and lubrication
- Incomplete sealing: Inspect seat surfaces and alignment
- Erratic operation: Evaluate control system signals and connections
For Diverter Valves:
- Stuck handles: Apply appropriate lubricant and check for mineral deposits
- Leaks: Replace worn seals or tighten connections
- Inconsistent flow: Clear debris from the valve body and ports
Preventive maintenance significantly extends the valve life. Implement a systematic approach that includes regular cleaning, lubrication, and parts replacement based on operating conditions and manufacturer recommendations. Document all maintenance activities and valve performance metrics to identify patterns and predict potential failures before they occur.
Conclusion
Selecting between transfer and diverter valves impacts system efficiency, maintenance requirements, and operational costs. Understanding their distinct capabilities ensures optimal performance across industrial and commercial applications.
While transfer valves excel in high-pressure, precision-demanding environments, diverter valves offer reliable solutions for more straightforward flow control needs. Each type brings unique advantages that make them invaluable in their respective applications.
For expert guidance on valve selection or to explore high-quality transfer and diverter valve solutions, contact Everlasting Valve today. Our engineering team will help you choose the correct valve for your requirements.