Stainless Steel Control Valve Selection Guide
04-07-25
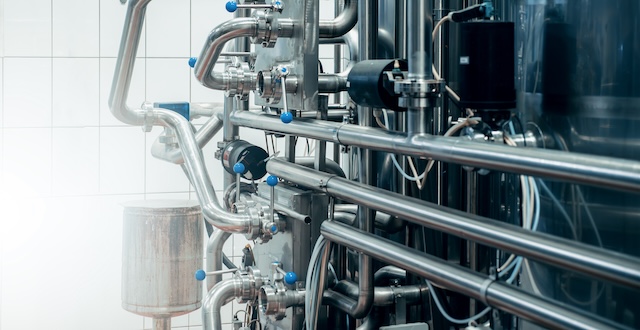
In industrial processes where reliability and longevity matter, selecting the right stainless steel control valve is critical to operational success. Control valves regulate the flow of media—whether liquid, gas, or slurry—and play a vital role in maintaining process efficiency and safety. This guide will help engineering and procurement professionals navigate the selection process to find the optimal stainless steel control valve for their specific applications.
Understanding Stainless Steel Control Valves
Stainless steel control valves are engineered to provide precise flow control while offering superior corrosion resistance compared to standard carbon steel alternatives. The stainless steel construction makes these valves particularly valuable in harsh environments where exposure to corrosive media, extreme temperatures, or abrasive materials is common.
The primary advantages of stainless steel control valves include:
- Exceptional corrosion resistance
- Extended service life in challenging environments
- Compliance with hygiene standards for food, beverage, and pharmaceutical applications
- Ability to withstand high temperatures
- Lower maintenance requirements and lifecycle costs
Key Factors in Stainless Steel Control Valve Selection
1. Process Media Characteristics
The properties of your process media significantly influence valve selection:
- Corrosiveness: For highly corrosive media, 316L stainless steel often provides superior performance
- Abrasiveness: When handling slurries or media with suspended solids, select valves with self-lapping capabilities
- Viscosity: Higher viscosity fluids may require specialized valve designs to maintain control precision
- Temperature range: Ensure the selected valve can handle both your normal operating temperatures and potential extremes
2. Flow Characteristics and Control Requirements
Different applications require specific flow characteristics:
- Equal percentage: Ideal for processes requiring precise control at low flow rates
- Linear: Suitable for applications where flow should change in direct proportion to valve position
- Quick-opening: Appropriate for on/off applications requiring rapid response
The rangeability (ratio between maximum and minimum controllable flow) is also crucial for applications with varying flow requirements.
3. Pressure Considerations
Several pressure-related factors affect valve selection:
- Operating pressure: The valve must withstand normal system pressure
- Pressure drop: The differential pressure across the valve impacts sizing and potential for cavitation
- Recovery characteristics: Critical for applications where pressure recovery could lead to flashing or cavitation
4. Stainless Steel Grade Selection
Different grades offer varying benefits:
- 304 stainless steel: Good general corrosion resistance at moderate cost
- 316/316L stainless steel: Enhanced resistance to chlorides and process chemicals
- Duplex stainless steel: Superior strength and stress corrosion cracking resistance
- Super-duplex and super-austenitic alloys: For extremely corrosive environments
5. Valve Body Design
Common stainless steel control valve body designs include:
- Globe valves: Versatile with excellent throttling capabilities
- Ball valves: Provide tight shutoff and handle particulates well
- Butterfly valves: Economical for larger pipe diameters
- Diaphragm valves: Ideal for sanitary applications
- Rotary process valves: Excellent for handling abrasive media and offering self-cleaning action
6. Actuator Selection
The actuator must match your control needs:
- Pneumatic actuators: Common, reliable, and intrinsically safe
- Electric actuators: Precise positioning without compressed air requirements
- Hydraulic actuators: High force capabilities for larger valves
- Manual operators: For infrequent adjustment or emergency backup
7. Industry-Specific Requirements
Different industries have unique needs:
- Chemical processing: Chemical compatibility and leak prevention are paramount
- Oil and gas: High-pressure capabilities and fire-safe designs
- Food and pharmaceutical: Sanitary design with appropriate surface finish and documentation
- Power generation: Temperature resistance and reliability under cycling conditions
- Mining: Extreme abrasion resistance and maintainability
Optimizing Total Cost of Ownership
When selecting a stainless steel control valve, consider the total cost of ownership, not just the initial purchase price. Factors affecting long-term costs include:
- Maintenance requirements and accessibility
- Spare parts availability and standardization
- Energy consumption through pressure drop
- Process downtime for valve service
- Potential for process disruption due to valve failure
Everlasting Valve’s Stainless Steel Control Valve Solutions
Everlasting Valve’s stainless steel control valves are engineered for the most demanding applications. Our unique self-lapping, rotating disc design provides several advantages:
- Improved sealing with each operation
- Exceptional durability in abrasive and high-temperature applications
- Reduced maintenance requirements
- Superior performance in challenging environments where conventional valves fail
Our valves are custom-engineered to meet the specific requirements of your application, ensuring optimal performance and longevity. The Everlasting difference is evident in applications where other valves require frequent maintenance or replacement.
Making the Final Selection
When finalizing your stainless steel control valve selection:
- Document your process conditions thoroughly
- Consider both normal operation and potential upset conditions
- Evaluate valve performance data for your specific application
- Consult with valve experts who understand your industry
- Request references for similar applications
- Review maintenance requirements and spare parts availability
- Consider standardization with existing equipment
Contact Everlasting Valve today to discuss your project requirements.