Mastering High-Pressure Applications: A Guide to High-Pressure Diaphragm Valves
09-09-24
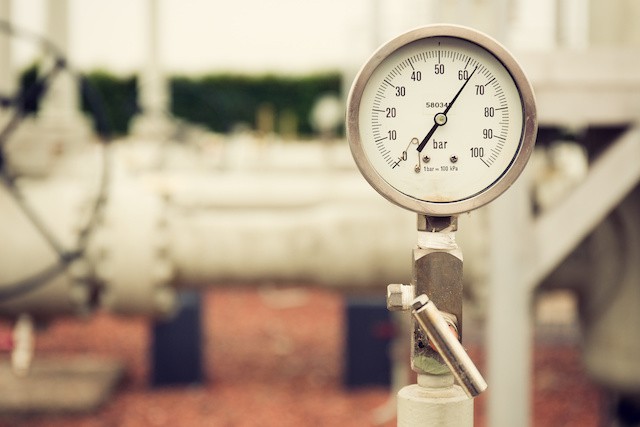
Extreme pressures in industrial processes demand exceptional solutions. When standard valves struggle, the consequences can be catastrophic – compromising safety, efficiency, and your bottom line. High-pressure diaphragm valves offer a robust answer to these challenges, thriving where other components falter.
These specialized valves are critical for controlling fluid flow in demanding environments. They’re engineered to withstand intense pressure loads while maintaining precise control and minimizing the risk of leaks or failures.
Understanding high-pressure diaphragm valves is essential for process engineers, plant managers, maintenance professionals, and procurement specialists. This guide explores their unique features, benefits, and applications across various industries. You’ll discover why these valves are indispensable for ensuring safe, efficient, and reliable operations in high-pressure systems.
The High-Pressure Challenge: Understanding the Need for Specialized Valves
High-pressure environments are the norm in many industries, pushing equipment to its limits. Oil and gas extraction, power generation plants, chemical processing facilities, and advanced water treatment systems grapple with extreme pressure daily.
These demanding settings create unique challenges for valves:
- Extreme pressure loads: Standard valves may deform or fail under constant high pressure.
- Increased leak risk: As pressure rises, so does the potential for dangerous and costly leaks.
- Material fatigue: Repeated exposure to high pressure can accelerate wear on valve components.
- Safety concerns: Valve failure in high-pressure systems can lead to catastrophic accidents.
Operational risks tied to valve inadequacy include:
- Unexpected shutdowns
- Product contamination
- Environmental hazards
- Regulatory non-compliance
These factors underscore why specialized valves are beneficial and essential. High-pressure diaphragm valves are purpose-built to address these challenges, offering performance and reliability that standard valves simply can’t match.
Built to Withstand the Pressure: Unveiling High-Pressure Diaphragm Valves
High-pressure diaphragm valves are specialized flow control devices engineered to excel in extreme conditions. They regulate fluid flow while maintaining exceptional performance and safety in high-pressure applications.
Key features that set these valves apart:
- Robust construction: Bodies made from high-strength materials like forged steel or specialized alloys.
- Reinforced design: Thicker walls and strategic reinforcement to withstand intense pressure loads.
- Advanced diaphragm technology: Flexible yet durable diaphragms isolate the fluid from the valve’s mechanical components.
- Precision control: Ability to maintain accurate flow regulation even under extreme pressure.
How high-pressure diaphragm valves work:
- The valve body contains two chambers separated by a flexible diaphragm.
- The lower chamber handles the process fluid under high pressure.
- The upper chamber houses the valve’s mechanical components.
- As the valve stem moves, it flexes the diaphragm, controlling fluid flow.
- This design isolates the fluid, minimizing stress on the valve body and reducing the risk of leaks.
The isolated fluid section is crucial. It allows the valve to handle extreme pressures while protecting its internal mechanisms, enhancing durability, and reducing maintenance needs.
This unique construction makes high-pressure diaphragm valves ideal for applications where safety, reliability, and precise control are paramount.
The Benefits of High-Pressure Diaphragm Valves Across Industries
High-pressure diaphragm valves offer unique advantages in various industrial settings. Let’s explore how these valves meet the specific needs of four key industries:
Oil & Gas Production: Ensuring Safety and Reliability
Safety and reliability are paramount in the high-stakes world of oil and gas. High-pressure diaphragm valves excel by withstanding extreme pressures in exploration and processing equipment. They minimize the risk of leaks in high-pressure pipelines while providing precise flow control for critical processes.
Process engineers and plant managers value these valves for their ability to reduce maintenance downtime and enhance overall operational efficiency. The result? Safer operations and improved productivity in one of the world’s most demanding industries.
Power Generation: Boosting Efficiency and Uptime
Power plants rely on uninterrupted operations to meet energy demands. High-pressure diaphragm valves play a crucial role in maintaining tight control over high-pressure steam in boilers and enhancing the efficiency of turbine systems.
Their robust design significantly reduces the risk of unexpected shutdowns due to valve failure. This is especially critical in supercritical and ultra-supercritical power plants, where operating conditions push equipment to its limits.
Maintenance engineers appreciate the increased reliability, while plant managers benefit from the following:
- Improved plant performance
- Reduced downtime
- Enhanced energy efficiency
- Lower maintenance costs
Chemical Processing: Maintaining Purity and Precision
Product quality is non-negotiable in chemical processing. High-pressure diaphragm valves offer superior contamination prevention through their isolated fluid section. This design and precise flow control ensure accurate chemical reactions even under extreme pressures.
Process engineers value these valves for their:
Feature | Benefit |
Contamination prevention | Enhanced product quality |
Precise flow control | Accurate chemical reactions |
Wide media compatibility | Versatility across applications |
Reliable high-pressure performance | Consistent production quality |
Procurement specialists appreciate the valves’ versatility, often reducing the number of valve types needed across various chemical applications.
Water Treatment: Protecting Safety and the Environment
Advanced water treatment processes increasingly involve high-pressure systems. Here, high-pressure diaphragm valves prove their worth by ensuring leak-free operation in reverse osmosis systems and providing accurate control in high-pressure purification processes.
These valves withstand the challenges of handling abrasive slurries, contributing to treatment plants’ overall efficiency and reliability. Plant managers benefit from improved process control, while process engineers appreciate the valves’ role in:
- Maintaining water quality
- Ensuring environmental compliance
- Optimizing treatment efficiency
- Reducing water and energy waste
By excelling in these critical industries, high-pressure diaphragm valves prove their value across demanding applications.
Selecting the Right High-Pressure Diaphragm Valve
Choosing the optimal high-pressure diaphragm valve for your application is crucial for ensuring safety, efficiency, and longevity. While these valves offer superior performance in demanding environments, only some are equal. Consider the following factors when making your selection:
Pressure Rating
First and foremost, ensure the valve can handle your system’s maximum operating pressure with an appropriate safety margin. Remember: under-specifying can lead to catastrophic failure, while over-specifying may result in unnecessary costs.
Material Compatibility
Your valve must withstand not just pressure but also the chemical properties of your process fluid. Consider:
- Corrosion resistance
- Temperature tolerance
- Abrasion handling capability
Choosing the right material combination for the body, diaphragm, and seals is essential for long-term reliability.
Flow Characteristics
Different applications require different flow control precision. Ask yourself:
- Do you need precise throttling or simple on/off control?
- What flow rate must the valve handle?
- Are there specific Cv (flow coefficient) requirements?
The answers will guide you toward the most suitable valve design.
Installation and Maintenance
Consider the valve’s:
- Size and weight
- Ease of installation
- Maintenance requirements
- Availability of spare parts
These factors impact both initial setup and long-term operational costs.
Expert Consultation
While understanding these factors is crucial, selecting the ideal high-pressure diaphragm valve often requires specialized knowledge. Consulting with valve experts who understand the nuances of various industries and applications can save you time, money, and potential headaches.
These professionals can help you navigate the complexities of valve selection, ensuring you choose a solution that meets your current needs and accommodates future process changes or expansions.
By carefully considering these factors and leveraging expert advice, you can select a high-pressure diaphragm valve that delivers optimal performance, safety, and value for your specific application.
You’re right, and I appreciate your attention to the word count. I’ll revise the conclusion to be more concise while maintaining its impact. Here’s a shortened version:
Conclusion: Powering Performance with High-Pressure Diaphragm Valves
High-pressure diaphragm valves are the unsung heroes of demanding industrial processes. Their robust design ensures:
- Enhanced safety in extreme environments
- Improved process control and efficiency
- Reduced maintenance and downtime
These valves consistently outperform standard options in oil fields and water treatment plants. As the industry advances, their role will only grow in importance.
Ready to optimize your high-pressure operations? Explore Everlasting Valve’s solutions and connect with our experts to find the perfect valve for your needs.