Chemical Ball Valves: A Comprehensive Guide for Industrial Professionals
10-14-24
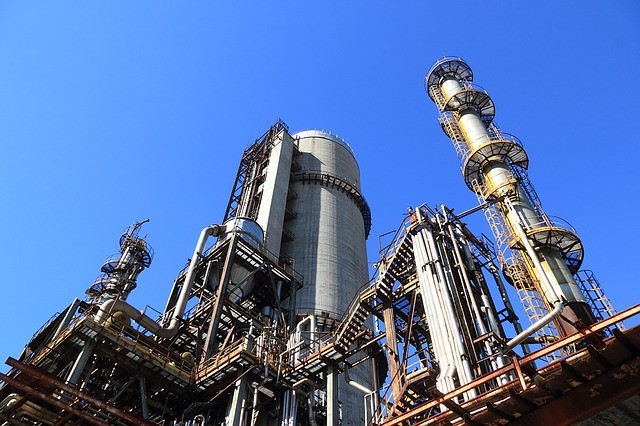
Leaks, downtime, and safety hazards are the nightmares that keep industrial professionals up at night. At the heart of many of these issues lies a critical component often overlooked until problems arise: the humble valve. Specifically, chemical ball valves are pivotal in controlling the flow of corrosive and hazardous materials across various industries.
For maintenance managers, persistent valve leakage isn’t just an annoyance; it’s a potential disaster waiting to happen. Reliability engineers are constantly seeking ways to reduce unplanned downtime and control costs. Meanwhile, procurement specialists are tasked with finding cost-effective solutions that maintain quality.
These challenges aren’t unique incidents – they’re daily realities for industrial professionals across the board. Whether you’re handling routine maintenance in a school building or overseeing critical processes in a healthcare facility, the right valve can make all the difference.
In this comprehensive guide, we’ll explore the world of chemical ball valves, their functionality, benefits, and how to select the perfect valve for your specific needs. By the end, you’ll be equipped with the knowledge to make informed decisions that can boost efficiency, cut costs, and enhance safety in your facility.
Understanding Chemical Ball Valves
At their core, chemical ball valves are precision-engineered marvels designed to control the flow of corrosive and aggressive fluids. But what sets them apart from other valve types?
Picture a sphere with a hole drilled through its center, nestled snugly inside a valve body. This sphere, or “ball,” is the heart of the chemical ball valve. The hole aligns with the flow path when the valve opens, allowing liquids or gases to pass through freely. Rotate the ball a quarter turn, and the solid part blocks the path, stopping the flow entirely.
Key components of a chemical ball valve include:
- Ball: The main sealing element, typically made of corrosion-resistant materials
- Seats: Soft or metal seals that ensure a tight closure
- Stem: Connects the ball to the external actuator
- Body: Houses all internal components and connects to the piping system
What makes these valves ideal for chemical applications? It’s all in the design:
- Full bore design allows unrestricted flow when open
- Quarter-turn operation enables quick shutoff in emergencies
- Bubble-tight sealing prevents leaks of hazardous materials
- A variety of material options to match specific chemical compatibility needs
Chemical ball valves offer a robust solution for those working in harsh industrial environments. They combine simplicity with high performance and are equally at home in a school’s water treatment system as they are in a pharmaceutical plant’s production line.
Understanding how these valves work is the first step in harnessing their potential to solve common industrial challenges. In the next section, we’ll explore the benefits of chemical ball valves being a go-to choice for professionals across various sectors.
Benefits of Chemical Ball Valves
Chemical ball valves aren’t just another tool in your industrial toolkit—they’re problem solvers that can significantly improve your operations. Let’s explore how these valves address common pain points across various industries:
- Durability and Longevity
-
-
- Resistant to corrosion and wear, even in harsh chemical environments
- Reduced need for frequent replacements, cutting down on maintenance costs
- Ideal for facilities looking to minimize disruptions and extend equipment life
-
- Cost-Effectiveness
-
-
- Lower initial investment compared to some specialized valve types
- Decreased maintenance and replacement expenses over time
- Energy-efficient operation due to minimal flow restriction when fully open
-
- Versatility
-
-
- Suitable for a wide range of chemicals, temperatures, and pressures
- Applicable in various industries, from water treatment to petrochemicals
- Available in different sizes and materials to fit specific application needs
-
- Safety Features
-
-
- Quick shut-off capability crucial for emergencies
- Reliable sealing to prevent leaks of hazardous materials
- Clear visual indication of valve position (open/closed) for easy monitoring
-
- Low Maintenance Requirements
-
-
- Simple design with fewer moving parts than many other valve types
- Easy to clean and service, reducing downtime for maintenance
- Self-cleaning action during operation helps maintain performance
-
- Precision Control
-
- Excellent throttling capabilities for accurate flow control
- Smooth operation allows for fine adjustments when needed
- Maintains tight shut-off even after thousands of cycles
Chemical ball valves offer a solution that balances performance, safety, and cost-effectiveness by addressing these key areas. Whether managing a large industrial plant or overseeing maintenance for a smaller facility, these benefits translate to improved efficiency and peace of mind.
Selecting the Right Chemical Ball Valve
Choosing the perfect chemical ball valve doesn’t have to be a headache. Let’s break down the key factors to consider:
Material Compatibility: Your First Line of Defense
The valve you choose must withstand the chemicals you’re handling. Stainless steel, PVC, PTFE-lined, and exotic alloys are all contenders, but the right choice depends on your specific needs. For top-notch performance, remember to consider both the ball and seat materials.
Pressure and Temperature: Know Your Limits
What’s the maximum pressure and temperature in your system? Pick a valve that exceeds these requirements for a safety cushion. Remember: pressure ratings often dip as temperatures rise, so factor that into your decision.
Flow Requirements: Size Matters
Calculate your required flow rate and choose a valve to match. Pay attention to the Cv (flow coefficient) value for precise control. Full-port valves offer minimal restrictions but might be bulkier and pricier. Weigh your options carefully.
Connection and Actuation: The Perfect Fit
Whether you need flanged, threaded, or welded connections, ensure compatibility with your existing setup. As for actuation, manual operation might work for rarely adjusted valves, while remote locations might call for pneumatic or electric options.
Certifications and Cost: The Long Game
Look for industry certifications like ANSI, API, or ISO for quality assurance. When it comes to cost, think long-term. A higher upfront investment might lead to significant savings through reduced maintenance and a longer lifespan.
By considering these factors, you’ll be well-equipped to choose a chemical ball valve that meets your current needs and provides reliable, efficient service for years to come.
Conclusion: Mastering Chemical Ball Valves
We’ve explored the world of chemical ball valves, from their inner workings to selection criteria. These versatile components offer durability, precision, and cost-effectiveness in harsh environments. By considering factors like material compatibility, pressure ratings, and long-term value, you can choose the perfect valve for your needs. Remember, the right chemical ball valve can solve persistent leaks, boost efficiency, and improve equipment performance.
But knowledge is just the first step. The real power lies in applying this information to your specific challenges. Every facility is unique, so evaluate your needs carefully and don’t hesitate to consult experts. As you progress, keep an eye on emerging valve technologies and industry trends. Your path to more efficient, safer, and cost-effective operations starts with the correct valve – and Everlasting Valve is here to help. Ready to find the perfect chemical ball valve for your application? Contact Everlasting Valve for expert guidance and top-quality solutions tailored to your needs.